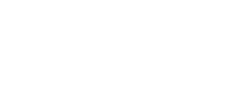
معرفی شرکت صنعتی و معدنی توسعه ملی سنگان
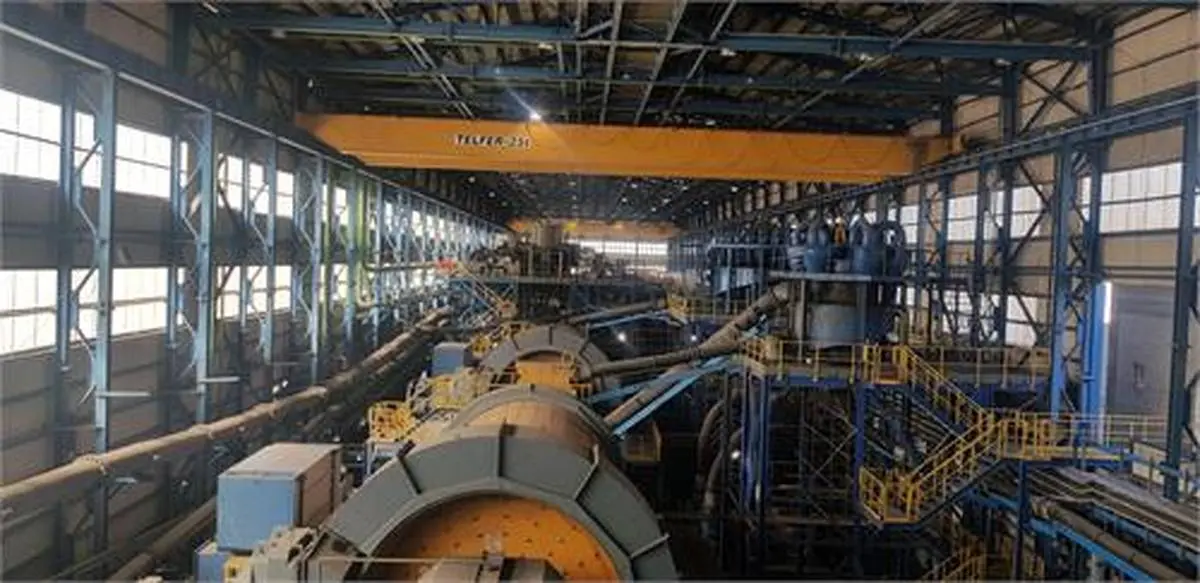
شرکت صنعتی و معدنی توسعه ملی با ظرفیت ۲.۵ میلیون تن در سال، کنسانتره تولید میکند. کنترل و افزایش عیار آهن موجود در سنگ، یکپارچگی ساختار ظاهری و داخلی سنگ از دلایل فرآوری سنگ آهن میباشد.
به گزارش شمانیوز:خردایش، آسیاکنی، پرعیارسازی، آبگیری یا خشک کردن، مراحل پرعیارسازی سنگ آهن و حذف عناصر زائد از سنگ آهن به شمار میرود. اولین مرحله در چرخه تولید کنسانتره با ورود سنگ آهن به سنگشکن آغاز میشود، سپس مواد معدنی خردایش شده توسط نوار نقاله به ناحیه بلندینگ کارخانه منتقل شده و مرحله انباشت و برداشت توسط استکر و ریکلایمر انجام و خوراکدهی به خط تولید شروع میشود. باتوجه به طراحی کارخانه در ابتدای خط ورودی خوراک به ناحیه ۱۱۴، یک سرند با سایز ورودی ۵۰-۰ میلیمتر قرار دارد که سنگ آهن با ابعاد بیشتر از سایز ذکر شده به عنوان سرریز از سرند خارج و جهت خردایش مجدد به واحدهای سنگ شکنی منتقل میگردد. سنگ آهن در ادامه چرخه تولید وارد آسیای غلطکی فشار بالا میگردد. در حال حاضر در کارخانههای فرآوری سنگ آهن، از این تجهیز برای تامین دو هدف عمده استفاده میگردد: پیش از مدار آسیاکنی با هدف پیش نرمکنی مواد سنگشکنی شده و در انتهای مدار فرآوری، با هدف افزایش عدد بلین کنسانتره جهت تامین خوراک مطلوب کارخانه گندلهسازی، محصول خروجی آسیای غلطکی فشار بالا وارد سرند ۶-۰ میلیمتری سالن تولید میگردد. شایان ذکر است با
افزودن آب در این قسمت فرایندها به صورتتر انجام میگردد. اسلاری خروجی سرند در ابتدا به منظور جداسازی به روش گریز از مرکز ذرات و بر اساس دانهبندی ریز یا درشت وارد هیدروسیکلون اولیه شده و ذرات کوچک به عنوان سرریز و ذرات درشت به عنوان تهریز خارج میگردند. ذرات درشت در ادامه چرخه تولید به منظور خردایش وارد بال میل اولیه میگردد. ذرات پس از عبور از مرحله آسیا کنی به ابعاد بسیار ریز مورد نظر رسیدهاند و لازم است به منظور جدا کردن مواد باارزش به اولین ناحیه جدایش مغناطیسی هدایت شوند. جداکنندههای مغناطیسیتر، عموماً جداکنندههای نوع درام هستند و اسلاری از روی این درامها که دارای خاصیت مغناطیسی میباشد عبور داده میشود. کانیهای آهندار به درام میچسبند و در انتهای درام توسط یک تیغه از روی درام جمعآوری میشوند. سایر کانیهای موجود در دوغاب نیز از تهریز تجهیز خارج و به حوضچه تیکنر انتقال یافته و کانیهای آهندار حاصله مجدداً جهت ادامه چرخه فرآیندی وارد هیدروسیکلون اولیه میشوند. ذراتریز که به صورت سرریز از هیدروسیکلون اولیه خارج شده، وارد هیدروسیکلون ثانویه میگردند. مجدداً بر اساس اندازه، خروجی هیدروسیکلون
شامل ذرات درشتتر به صورت تهریز (وارد بال میل ثانویه شده و خردایش مجدد انجام شده و محصول مجدداً وارد هیدروسیکلون ثانویه میگردد) و ذرات ریز به صورت سرریز به منظور جدا کردن مواد باارزش به ناحیه جدایش مغناطیسی هدایت میشوند. کانیهای آهندار به درام میچسبند و سایر کانیهای موجود در دوغاب نیز از تهریز تجهیز خارج و به حوضچه تیکنر انتقال مییابد. کانیهای آهندار حاصله مجدداً جهت ادامه چرخه فرآیندی به منظور حذف عناصر مزاحم مانند گوگرد وارد سیستم فلوتاسیون میشود. در این مرحله گوگرد پس از عبور از سلولهای فلوتاسیون با اضافه نمودن مواد شیمیایی حذف میشود. در ادامه چرخه تولید، اسلاری حاصله به ناحیه جدایش مغناطیسی نهایی وارد میشود. کانیهای آهندار به درام میچسبند و به ناحیه فیلتراسیون منتقل میشود. سایر کانیهای موجود در دوغاب نیز از ته ریز تجهیز خارج و به دلیل دارا بودن مقدار قابل توجه آهن جهت جداسازی به ناحیه (Rougher) انتقال مییابد. اسلاری حاصله حاوی مقادیر زیادی آب است که باید آبگیری و خشک گردد و رطوبت آن به ۱۰-۹ درصد برسد. بدین منظور از فیلترهایی که به صورت دیسک فیلتر با صفحات سرامیکی میباشد برای خشک
کردن کنسانتره بدست آمده، استفاده میشود. سپس کنسانتره آبگیری شده به انبار محصول منتقل و در آنجا دپو میگردد. سایر کانیهای موجود در سنگ آهن که به صورت باطله به حوضچه تیکنر هدایت شدهاند توسط ماده شیمیایی به نام فلوکولانت تهنشین میشود. سرریز آب حاصله وارد چرخه تولید و ذرات جامد تهنشین شده به سمت سد باطله هدایت میشود. شایان ذکر است بر اساس طراحی کارخانه درصد عیار سنگ آهن در خوراک ورودی کارخانه ۴۲ درصد بوده که عیار کنسانتره خروجی باید ۶۷.۵ میباشد که در حال حاضر عیار کنسانتره خروجی بیشتر از ۶۹ میباشد.
منبع:فولاد خوزستان